Разделы: |
 |
 |
|
Термическая обработка металла
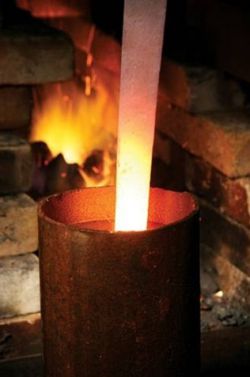 Термическая обработка металлов - это процесс тепловой обработки сплавов и металлов в целях придания им заданных свойств и структуры. Термическая обработка металлов делится на термомеханическую и химико- термическую.
Собственно термическим процессом обработки металлов является изменение их внутреннего строения путем нагрева, а после выдержки и в последствии быстрого охлаждения для получения нужных механико-физических свойств материалов. Основными типами термической обработки является закалка, отжиг, а также отпуск.
Термическая обработка металлов химией представляет собой насыщения поверхности материалов различного рода элементами, которые повышают твердость, коррозийную стойкость и износостойкость. Этот процесс требует длительных выдержек и повышенных температур. Наиболее распространенные способы химико-термической обработки – это азотирование( преобладает азотом), цементация ( преобладает углеродом), диффузионная металлизация, цианирование( одновременно насыщение азотом и углеродом) или поверхностное легирование. Поверхностное легирование в зависимости от насыщающего материала подразделяют на алитирование, хромирование, силицирование( насыщение алюминием, кремнием и хромом) и др.
Термомеханическая обработка металлов - является новым методом обработки металлов , который позволяет увеличить механические свойства в сравнении с полученными при обычном отпуске или закалке. Она производится с помощью пластичной деформации, в присутствии термообработки.
Основные виды термической обработки сталей, отличаются режимами термообработки, то есть выдержкой, температурой нагрева и скоростью охлаждения.
Изменения внутренней структуры стали полностью зависит от содержащегося в ней количества углерода. В связи с этим, выбор нагрева производят после тщательной проверки наличия углерода.
Отжиг – это процесс нагрева стали до температуры, которая определяет цель отжига, выдержку и в последствии охлаждение. Цель процесса отжига – это понижение твердости для более легкой механической обработки, устранения химической неоднородности стали и др. Полный отжиг производится путем нагрева материала на 40-50 градусов больше определяемых линий GSK, выдержка для этой температуры и в последствии охлаждения. Время выдержки, обязательно должно быть достаточным для нагрева материала по всему сечению.
 Закалка - производится с помощью нагрева стали до температуры выше 40-50 градусов линии GSK c последовательным быстрым охлаждением. Целью закалки является увеличение прочности и твердости стали.
Кроме обычной полной закалки стали производят еще и поверхностную. Самая распространенная поверхностная закалка стали – это закалка токами высокой частоты, которая производится с помощью специальных генераторов, подающих переменный ток на материал частотой 10 млн. герц. Нагрев материала производится индуктором, ко которому проходят токи высокой частоты.
Индуктор индуцирует токи в изделия, помещенное в внутри него. Обычно такой индуктор изготавливаю из полых медных трубок, по которым циркулирует вода и благодаря этому методу сам индуктор никогда не нагревается. Для того, чтобы нагрев производился равномерно по всей поверхности детали, форма индуктора должна быть подобна форме изделия.
Во время процесса отпуска уже закаленная сталь подвергается нагреву ниже температурной линии PSK, выдерживается при ней же и охлаждается в масле или на воздухе. Главная цель отпуска – это повысить прочность закаляемой стали. Температура нагревания при отпуске колеблется от 90 до 600 градусов. Выбор такой или иной температуры зависит от изготовляемой детали. При повышении температуры понижается прочность и твердость закаляемой стали, а вязкость увеличивается. На практике при термообработки различают 3 вида отпуска: низкий, который выполняется при температуре до 250 С, средний – при температуре до 450 С и высокой – при температуре до 650 С. Высокий отпуск полностью обеспечивает снятие остаточных напряжений, достаточную прочность и высокую вязкость стали.
При термической обработки металлов используют специальные оборудования, которые состоят из нагревательных устройств, различного рода приспособлений ( закалочные клещи, бачки с маслом и водой, и т.д.) и приборов для контроля режима тепла и результатов самой термической обработки . Из нагревательных устройств в основном используются печи, работающие на газообразном или жидком топливе или муфельные печи. Для охлаждения служит масло, воздух, растворы солей и вода.
Для контроля термического режима чаще всего применяют термоэлектрические пирометры, состоящие из гальванометра со шкалой в градусах Цельсия и из термопары.
Полученные результаты термической обработки металлов можно проверить напильником или твердомерами, которые определяют твердость стали, а так же испытанием на ударную вязкость.
Разновидность полного отжига заключается в нормализации , которая заключается в нагреве стали 40-50 градусов выше определяемой линии GSK, выдержки и последующего охлаждения на воздухе. Нормализация проводится для выравнивания его структуры и снятия напряжения в металле.
Закалка - производится с помощью нагрева стали до температуры выше 40-50 градусов линии GSK c последовательным быстрым охлаждением. Целью закалки является увеличение прочности и твердости стали.
Также используют и поверхностную закалку стали. Самая распространенная поверхностная закалка стали – это закалка высокой частоты токами, которая производится с помощью специальных генераторов, подающих переменный ток на материал частотой 10-12 млн. герц. Индуктором производится нагрев изделия, через который проходит ток с высокой частотой.
Токи в изделии индуцирует индуктор, помещенный в него. Обычно такой индуктор изготавливаю из полых трубок из меди и по ним циркулирует вода. В связи с этим сам индуктор никогда не нагревается. Для того, чтобы нагрев производился плавно по всей верхней части детали, форма индуктора должна быть подобна форме изделия.
Во время процесса отпуска уже закаленная сталь подвергается нагреву ниже температурной линии PSK, выдерживается при ней же и охлаждается в масле или на воздухе. Главная цель отпуска – это повысить прочность закаляемой стали. Температура нагревания при отпуске колеблется от 90 до 600 градусов. Выбор одной или другой температуры зависит от предназначения будущей детали. Если повысить температуру, то понижается прочность и твердость закаляемой стали, но увеличивается вязкость. При термообработки обозначают 3 типа отпуска: низкий, выполняющийся при температуре до 250 С, средний – при температуре до 450 С и высокой – при температуре до 650 С. Высокий отпуск полностью обеспечивает снятие остаточных напряжений, достаточную прочность и высокую вязкость стали.
При термической металлообработки используют специальные оборудования, которые состоят из нагревательных устройств, различного рода приспособлений ( закалочные клещи, бачки с маслом и водой, и т.д.), а также специальных приборов работающих для контроля режима тепла и результатов самой термической металлообработкой . Печи – главные нагревательные устройства, работающие на газообразном или жидком топливе или муфельные печи. Для охлаждения служит масло, воздух, растворы солей и вода.
Для контроля термического режима чаще всего применяют термоэлектрические пирометры, состоящие из гальванометра в градусах Цельсия и из термопары.
Полученные результаты термической обработки металлов можно проверить напильником или твердомерами, которые определяют твердость стали, а так же испытанием на ударную вязкость.
|